Diaphragm wall methods
Since the mid-1980s, hardly any other method has changed specialist foundation engineering as markedly as the technology of diaphragm wall equipment. One milestone was the introduction of the first Bauer trench cutter in 1984/85. Since then, diaphragm walls have become a standard method in specialist foundation engineering. Today they act as retaining structures or cut-off walls – for example to enclose excavation pits or to seal dams – or as foundation elements with a structural function.
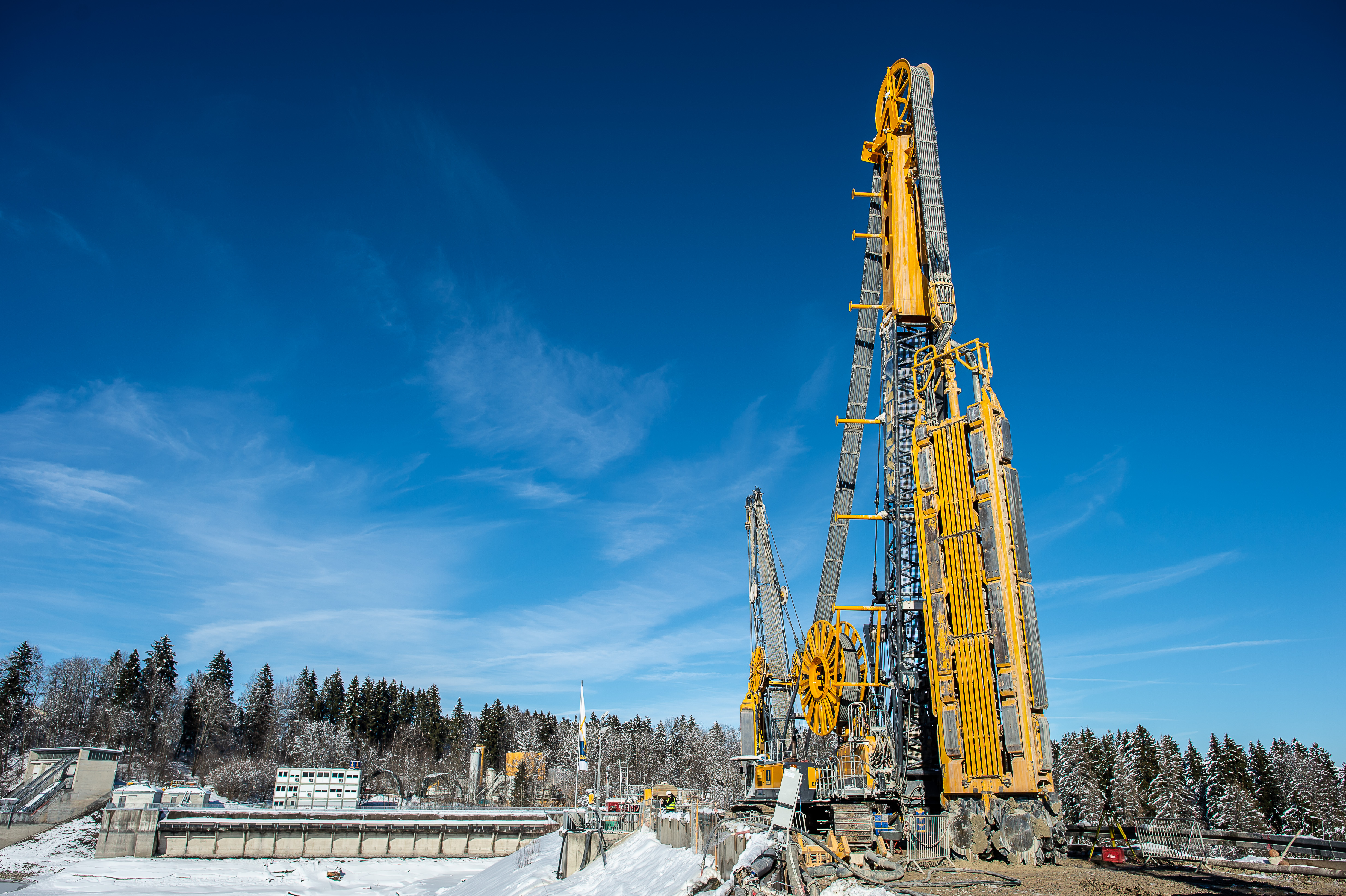
How is a diaphragm wall constructed?
Diaphragm wall with cutter
Trench cutters are especially used in hard or very hard soil conditions and with large trench depths. With this method, cutting wheels loosen the existing material, which is mixed with the slurry in the trench. A mud pump anchored in the cutting frame transports the material dissolved in the slurry upwards. Then the loaded slurry passes through a desanding plant. During this step, the solids are separated from the support slurry. At the same time, the slurry is pumped back into the slurry circuit for reuse and is made available again. The excavation of the slurry-supported trench continues without interruption during this time. TRecord depths of more than 250 m have already been achieved with the BC cutters from Bauer.
Diaphragm wall with grab
With the DHG (Diaphragm Hydraulic Grab) method, excavation is carried out in cycles. A cycle consists of inserting the grab into the trench, loosening the soil at the base and removing the dissolved soil material. Here as well, a support slurry stabilizes the open trench. After the trench is completed, joint elements and the reinforcement cage are inserted into the trench, which is concreted in an additional step. The slurry which is displaced in the process passes through the desanding plant and is fed into the slurry circuit to be reused. With Bauer’s DHG V diaphragm wall grab, trench lengths of up to 3,800 mm and trench widths of up to 1,500 mm are possible.
BAUER Cube System
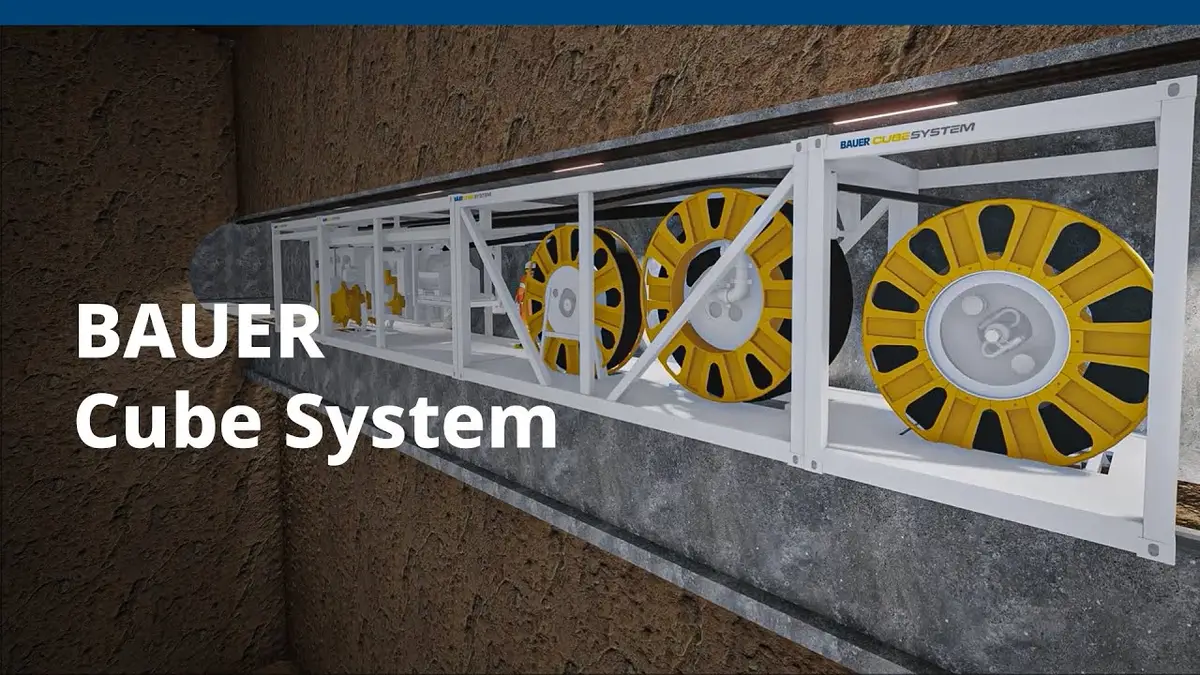